Prevent Problems Because of Mismatched Components
Virtually every Ferrotec vacuum rotary seal customer connects their feedthrough to a motor. In most applications, this integration process requires the customer to identify and source a motor that meets their specifications and then physically couple the motor with the spindle of their Ferrofluidic seal. In addition to the time and effort required to integrate the two components, this approach introduces potential failure points.
Problems can arise from backlash in transmissions or couplings, mismatched components or power ratings, poor precision, or drive components that just don’t fit.
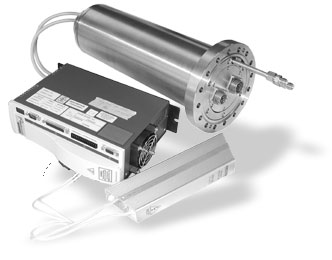
A Better Solution: In-line Drive Motorized Feedthroughs
With Ferrotec’s motor-integrated feedthroughs, you don’t have to wrestle with integration challenges and potential failure points. FerroDrive motorized spindles from Ferrotec combine a hermetic Ferrofluidic® vacuum feedthrough with a high precision motor and controller to offer a compact and high performance integrated sealing and rotation system. Ferrotec’s motor-integrated feedthroughs eliminate integration challenges and the potential mechanical failure points associated with coupling discrete components. In addition motor-integrated feedthroughs offer some exciting benefits:
Reduced size
An in-line motorized feedthrough is compact in comparison to an offset or shaft-coupled drive.
Integrated components
Ferrofluidic in-line motorized feedthroughs feature a brushless servomotor and matching amplifier with power supply and sinusoidal commutation. Application appropriate feedback devices and command loops are incorporated.
Improved performance
As the feedthrough has the motor fully integrated around the shaft rather than coupled to it, it provides optimum drive-to-load torque efficiency with no backlash over the life of the product.
Flexible configurations
Direct drive feedthroughs are available with either solid or hollow shafts.
Reduced implementation time
Supplied ready to install, a FerroDrive saves you time and effort in choosing and integrating components.
Ferrotec’s FerroDrive System
Typical applications that in-line drive motorized feedthroughs are used for include:
- Thin film
- Optical coating
- Ion beam deposition
- Ion beam etch
- PVD
- Sputtering
- Ion implantation
- Any application where a motor is used, particularly where servo control is necessary
FerroDrives are offered with hollow or solid shafts in sizes up to 2″ (50mm). Two different versions are available—a basic motorized spindle which uses a standard controller and Hall effect sensors for simple velocity control (within 2%), and a high precision version which features an encoder and advanced digital controller for extremely accurate speed and position control (within 0.01% or better).
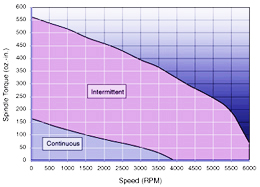
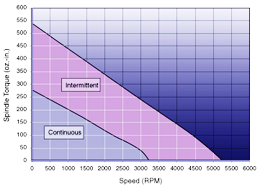
Products, Performance and Specifications
This data represents the performance of the complete FerroDrive (motor, feed-through and drive), not simply the motor in isolation.
Up to 1″ shaft size | Up to 2″ shaft size | |||
---|---|---|---|---|
Continuous Stall Torque | Tc | oz.·in. | 205 | 550 |
Continuous Stall Current | Ic | A | 3.6 | 10 |
Peak Torque | Tp | oz.·in. | 562 | 1075 |
Peak Current | Ip | A | 10 | 20 |
Torque Sensitivity (stall) | Kt | oz.·in./A | 56.8 | 54.8 |
Max. load* | P | lbs | 125 | 225 |
* maximum radial load on process end of shaft 1″ from flange
Customization
In addition to our standard FerroDrive products we can offer application-specific models. These may include features such as large diameters (up to 6"), shaft modifications, water cooled motors and various positioning options including higher resolution encoders and other types of positioning and control devices such as limit switches.
Do You Need More Information?
Find out more about Ferrotec’s Ferrofluidic Seals capabilities