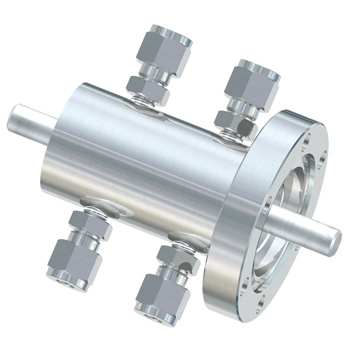
Vacuum Rotary Feedthroughs
Ferrotec is the world’s leading provider of vacuum rotary feedthroughs. We offer a broad range of vacuum rotary feedthroughs and Ferrofluidic® seals ranging from standard sizes and configurations to custom seals that have been designed specifically to meet demanding application requirements.
- Standard Feedthroughs — seals that fit most common applications
- Modified Standard Feedthroughs — add unique features for your requirements
- Retrofits — re-engineered seal subcomponents for classic equipment
- Custom Designs — solve your unique motion seal application
- Subsystem Assemblies — turnkey supply of complete equipment subsystems
- Repairs — expert feedthrough repair services
Select a Product Matching Your Requirements
Click the graphic that best represents the type of feedthrough or seal you’re looking for. A text description of each product will display if you simply roll your mouse over the graphic.
Using a Standard Feedthrough as a Template
Our standard designs are often used as a template. While your requirements may almost fit one of our standard parts, our standard part may not be exactly what you need. Not all standard applications look the same, but it’s usually not difficult for us to make modifications to a standard Ferrotec design in order to meet your requirements. Common modifications include shaft length and mounting hole changes.
To modify a standard feedthrough, start by identifying the standard feedthrough that you want to base the design on. Once you have selected the correct part, contact your Ferrotec representative (either directly or using the form provided on the Ordering Information page), and we can work with you to specify the necessary changes.
Click the graphic that best represents the type of feedthrough or seal you’re looking for. A text description of each product will display if you simply roll your mouse over the graphic.
Retrofit and Upgrade Solutions for Vacuum Manufacturing Systems
As the industry leader in rotary seals, Ferrotec understands the requirements of your performance application. Although some equipment may not have been originally designed using a Ferrofluidic seal, a solution from Ferrotec can eliminate operational hassles and improve system performance.
Ferrotec offers retrofit and upgrade solutions for many vacuum manufacturing systems. If you don’t see your specific system listed, contact your Ferrotec representative and find out about the solution that is right for you.
Popular Examples
Varian 3000-series Sputtering System
Non-contacting Ferrofluidic seals improve uptime and extend the tool’s productive life. Smooth mechanical operation eliminates binding and drag, and reduced particles and contaminants improve product quality.
Oerlikon / Unaxis Z 660, Zh 620, Vanguard, Emerald and Corona Sputtering Tool
Ferrotec’s engineered solution upgrades the rotary-lift subassembly while providing a complete refurbishment. Eliminate electrical arcing, improve plasma stability and process repeatability, and extend tool operation and uptime.
Tokyo Electron Alpha-8, -8S and -8SE CVD Furnace
Hermetic Ferrofluidic seals eliminate environmental leaks and contamination. Ferrotec’s high performance retrofit provides long life and high reliability.
Perkin Elmer 4400-series Sputtering System
Ferrotec offers several individual feedthroughs as well as full upgrade and refurbishment of the rotary-lift subassembly. The original design’s elastomer seals cause binding and leaks and lead to unplanned downtime and maintenance. Replace the old parts with proven Ferrofluidic seals and an easily serviceable commercial water union.
We Specialize in Engineering Solutions
At Ferrotec, we’re committed to providing solutions that make your products work better, more precisely, and more reliably. When the challenges of your application exceed the specifications of our standard products, we can work with you to engineer a customized solution specifically suited to your unique application challenges.
From simple modifications of our standard products to custom-engineered precision-motion assemblies for new applications, we specialize in engineering solutions.
Many feedthrough parameters can be modified or customized to ensure that the final product matches your application. Some common customized features include:
Size and Shape
- Small diameter or short length designs
- Large diameter or long shaft designs
- Fit within existing envelopes
Motion
- Multi-axial rotation
- Rotary and linear motion
- Integrated motor, gear drive, or drive coupling
Mounting, Seal and Housing Configuration
- Alternative materials
- Surface finishes and coatings
- Customized flanges
- Location of sealing stages (on the stator or rotor)
Performance Features
- Ferrofluid type
- External magnetic field
- Bearing type, material, and position
Shaft Features and Performance
- Shaft strength
- Shaft termination features
- Shaft material
- Material combinations
- Coatings, surface finishes
Performance Features
- Ferrofluid type
- External magnetic field
- Bearing type, material, and position
Subsystem Integration Design and Assembly
- End effectors and components
- Motor, in-line drive, and Ferrodrive integration
- Advanced features to integrate with complex tools
Custom Design Examples
Many feedthrough parameters can be modified or customized to ensure that the final product matches your application. Some common customized features include:
With over thirty years of experience developing and manufacturing precision sealing solutions for our customers, Ferrotec has developed custom solutions for many of the world’s most demanding applications. Here are some common examples of custom engineered feedthroughs and sealing sub-systems that we have developed.
Compact Designs
Ferrotec offers extremely compact seals with small seal envelopes. These are sometimes the only option in the case of retrofits where there is limited axial or radial space available. In new designs they are often beneficial to the overall system layout.
Typical applications that Ferrotec’s compact designs are used for include:
- FLIR devices
- Retrofit feedthroughs
- Rinser-dryers
High-speed, Large Diameter Hollow Shaft Feedthroughs
High speed, large diameter hollow shaft feedthroughs are ideal for optical coating applications, e.g. fiber optic filter manufacturing. These feedthroughs are configured with a double Ferrofluidic seal to enable static access to the rear of the seal. Drive is supplied via a toothed belt through the side of the housing or an integral brushless motor within the feedthrough housing. The product can then be accurately observed or measured through the large diameter hollow shaft without the difficulties associated with a rotating window. Seals with an 8″ internal diameter can be used at speeds up to 1,000 rpm.
Typical applications of high-speed, large diameter hollow shaft feedthroughs include:
- Optical coating applications
- 300 mm wafer rotation mechanisms
Multi-axial Feedthroughs
Ferrotec offers multi-axial feedthroughs for wafer handling applications. These offer extremely high repeatability with zero backlash. Linear motion is often incorporated as is cantilevered bearing configuration to optimize for UHV (Ultra High Vacuum) applications. Unlike magnetic couplings, the feedthroughs employ a continuous shaft per axis to transmit torque to the load, so torsional stiffness is maximized, allowing for the highest torque transmission of any UHV wafer-handling rotary seal technology.
Typical applications of multi-axial feedthroughs include:
- Wafer handling
- CVD wafer rotation with stationary inner shaft
Rotary-linear Feedthroughs
Rotary linear feedthroughs integrate a Ferrofluidic rotary seal with an edge-welded metal bellows linear seal. They use pre-loaded angular contact rotary bearings and sleeve or ball-type linear bearings. Such feedthroughs are ideal for wafer handling and aligning applications where precise indexing and translation are involved.
Typical applications of rotary-linear feedthroughs include:
- Wafer handling and alignment with Z-motion
High-precision Spindle Design
Ferrofluidic spindles can be engineered to rotate with as little as 0.0001″ (0.005 mm) of run-out. These products are ideal for high precision wafer handling/aligning applications and wafer/substrate rotation applications where wobble requirements are very stringent. Axial, radial and torsional spindle stiffness are achieved by custom engineering the bearing and shaft designs.
Typical applications that Ferrotec’s high-precision spindle designs are used for include:
- Wafer handling
- Ion implantation
In-line Drive Motorized Feedthroughs
An in-line motorized feedthrough is compact in comparison to an offset or shaft-coupled drive. Ferrofluidic in-line motorized feedthroughs feature a brushless servomotor and matching amplifier with power supply and sinusoidal commutation. Application appropriate feedback devices and command loops are incorporated. As the feedthrough has the motor fully integrated around the shaft rather than coupled to it, it provides optimum drive-to-load torque efficiency over the life of the product. Direct drive feedthroughs are available with either solid or hollow shafts.
Typical applications that in-line drive motorized feedthroughs are used for include:
- Any application where a motor is used, particularly where servo control is necessary
Rotary Gas Unions
Ferrofluidic rotary gas unions offer manufacturers of Chemical Vapor Deposition (CVD) and other deposition systems an efficient and flexible method of introducing gases into a process. A static gas feed runs into the rotating shaft which supports the wafer. This ensures that the gas outlet is in the center of the wafer, resulting in uniform coating characteristics.
More information on Rotary Gas Unions can be found in the Gas and Vacuum Unions section of the Ferrotec web site. Read More »
Reactive Gas Seal
Reactive gas seals for applications such as MOCVD use an inert fluorocarbon based fluid. They feature a cantilevered seal design to protect the bearings from process gases. Special materials are used in the seal construction. Inert gas purges or protective plating can also be added to prevent corrosive attack of seal components.
More information on Reactive Gas Seals can be found in the Gas and Vacuum Unions section of the Ferrotec web site. Read More »
Retrofit Feedthroughs
Ferrotec offers a range of retrofit feedthroughs that we’ve already designed for many vacuum systems supplied by leading semiconductor OEMs. If your part isn’t in our existing library of retrofit designs, we can design and optimize a retrofit seal to replace your current part with a Ferrofluidic seal.
More information about Ferrotec’s Retrofit Feedthroughs can be found on the Retrofit Seals page of the Ferrotec web site. Read More »
We will Work With You to Modify Standard Ferrotec Designs
Our standard feedthrough designs are often used as a custom design template. While your requirements may almost fit one of our standard parts, our standard part may not be exactly what you need. Not all standard applications look the same, but it’s usually not difficult for us to make modifications to a standard Ferrotec design in order to meet your requirements. Common modifications include shaft length and mounting hole changes.
To modify a standard feedthrough, start by identifying the standard feedthrough that you want to base the design on. Once you have selected the correct part, contact your Ferrotec representative (either directly or using the form provided on the Ordering Information page), and we can work with you to specify the necessary changes.
If you have questions about pricing and availability, need more information about Ferrotec’s rotary feedthroughs, or if you have other Ferrofluidic seal requirements, you can submit your request using the form below or contact your Ferrotec representative directly »
Special Orders, Modifications, and Customized Solutions for Unique Applications
We Can Help Streamline Your Components
Discover the benefits of having Ferrotec become your engineering partner. With our extensive experience in vacuum manufacturing, sealing and robotic systems, Ferrotec can help you integrate your components into streamlined sub-assemblies that deliver measurable product benefits.
Reduce your design & development time
Partnering with Ferrotec enables your internal engineering staff to focus on the core development of your product.
Reduce your costs
From motorized integrated drive-throughs to closely matching component selections, when we are able to look at your entire engineering challenge, we can engineer an integrated product that performs better.
From concept to completion, Ferrotec offers the engineering, design and manufacturing capabilities to ensure that your sealing sub-system delivers world-class performance. Ferrotec was the first company to manufacture magnetic liquid seals and has spent the last 30 years further developing and advancing the technology. With 30 years’ proven track record of supplying seals to the semiconductor, optical, aero-space, medical, defense, lamp manufacturing and other industries you can be sure that our expertise is second to none. Whether you need us to manufacture to an existing sub-system design, or need a new state-of-the-art Ferrotec custom design, Ferrotec is your ideal partner for expertly manufactured and tested sealing sub-assemblies, shipped dock-to-stock to meet your production needs.
We apply the same stringent manufacturing and control processes developed for our Ferrofluidic® seals to all our sub-systems. Our design engineers work closely with you to develop a thorough product specification.
Manufacturing engineers develop detailed procedures to ensure that all specifications are met and a complete manufacturing control document is produced. Each part in the assembly is carefully inspected using the most advanced quality practices and thoroughly cleaned before assembly in our cleanroom. Highly skilled manufacturing technicians assemble your sub-system with care and precision. Finally, completed assemblies are thoroughly inspected and tested to ensure that all operational and dimensional specifications are correct before shipping to your manufacturing floor.
Ferrotec’s Sub-system Manufacturing Experience
Ferrotec has experience manufacturing a broad range of subsystems for semiconductor, optical, aerospace, medical, defense, lamp manufacturing and other applications. Some examples include:
Servo-controlled rotary feedthroughs
A custom servo-controlled rotary feedthrough offers precise speed and position control by combining servo control and high resolution encoder feedback with a non-wearing high vacuum Ferrofluidic rotary feedthrough. Speed accuracy of ±0.1% is combined with smooth rotation.
Servo-controlled rotary linear coaxial Ferrofluidic feedthroughs with precision position control
These sub-systems combine non-wearing Ferrofluidic rotary sealing with smooth linear actuation. Servo control with high resolution encoder feedback offers precise speed, positioning and indexing control. It also offers high load capacity and torsional stiffness.
Wafer handling arm
The wafer handling arm sub-assembly is integrated into a cluster tool where it positions 200mm and 300mm wafers, picking and placing them at different locations for processing. The sub-assembly features a Ferrofluidic coaxial feedthrough powered by a brushed DC motor and a harmonic drive, directly integrated with the precision in-vacuum components and other hardware demanded by the system.
Rotary Linear Wafer Positioner
Ferrotec built this 300mm rotary linear wafer positioning assembly to a customer’s existing design and specification. The sub-system picks up, rotates and lowers the wafers, providing motion in the z-axis as well as rotary motion. Initially Ferrotec worked closely with the customer to develop a Ferrofluidic seal for this application. Ferrotec later value engineered and manufactured the complete sub-system, and now takes care of part procurement, supply chain management, building and testing the system.